Ever since it was founded, Breizh PR, an automotive spare parts platform for professionals located in the Kerjean business park in Rostrenen (Côtes d'Armor), has relied on Savoye's digital solutions and technologies to support its development.
At the beginning of July 2017, the Breizh PR multi-brand automotive spare parts platform inaugurated its 7400 m² storage facility in the Kerjean business park in Rostrenen, Brittany. Created via a partnership of four investors, Breizh PR is a member of the Distrigo network, which brings together 39 platforms for the marketing and distribution of PSA and multi-brand spare parts, as well as tires. This hub stores nearly 40,000 different catalog numbers of Peugeot, Citroën, DS and PSA vehicle parts, as well as an all-brand range, which it distributes throughout Brittany.
The distribution of automotive parts is a very demanding sector, requiring high responsiveness to ensure increasingly short delivery times and increasingly late cutoffs, so it must be able to rely on robust and flexible logistics. “Service is the key element in this sector. It is therefore essential to be able to adapt to the varying flows and to absorb the order volumes at all times,” explains Julien Le Floch’, Director of Breizh PR. “That is why, from the outset of the project, we wanted to work with an expert like Savoye that would be able to offer us a smart automated system to suit the demands of our business,” he continues.
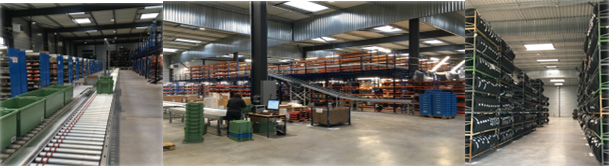
The logistic plattform in Rostrenen (Côtes d'Armor)
A smart conveyor at the heart of demanding logistics
Being equipped with a DMS (Dealer Management System) from Reynolds & Reynolds, a company working in partnership with Savoye, it is natural that Breizh PR would turn to Savoye, the designer and integrator of logistics solutions, to set up the Intelis modular conveyor system, combined with Logys WMS, on its site. “In addition to facilitating the interoperability of the systems, Savoye has a great deal of experience in our business sector, and the dedicated project team gave us the advice and attention we needed to complete the project successfully,” adds Mickaël Touchard, Chief Operating Officer of Breizh PR.
As of 2016, the mezzanine was designed and built around the conveyor system, which is considered to be the nerve center of the platform. When it opened in July 2017, 25,000 catalog items passed through it, i.e. 60% of orders. Gradually, 70%, then 74%, of the flows were carried by the conveyor, approaching the 80% target. There are currently 3500 lines prepared daily on site, and 2000 parcels shipped in just a few hours. Cross-docking preparation was also implemented for urgent orders. The conveyor, combined with a scheduling system, identifies the urgency of preparation, assigns parts to the right place, and then routes packages to the shipping docks. “The system was quickly able to reduce vehicle downtime, ensure better delivery times, and improve the service rate. We achieve service rates of 91% on D day and 99% on D+1,” points out Mickaël Touchard.
Consulting and modularity to support growth
At the same time, the system installed by Savoye also made it possible to optimize the movements of operators, thus reducing the risk of MSDs. During the Covid-19 crisis, the tool also demonstrated its flexibility, allowing large order flows to be absorbed as soon as operations were resumed, but also enabling the continuous growth of the company. “We have grown from a turnover of 40 million in 2018 to 65 million in 2020. We are also planning to expand our existing building and rethink our conveyor system to adapt to these changes. Savoye is attentive to our needs and has the capacity to support us. Our partnership has become a part of our daily life as we progress in our growth areas,” concludes Julien Le Floch’, director of Breizh PR.